Successful Design Scheduling
Christopher W. Carson, CEP DRMP PSP FAACE;
Aaron Fletcher, PSP; Noah A. Jones, PSP;
and Leo Carson-Penalosa
Abstract–Delays often originate within the architectural and engineering (A/E) design effort. The schedules developed to plan, organize, and monitor design tend to be high-level and not very effective to accurately model the work at a level of detail that allows for on time, on budget, and quality completion. When the schedule does not provide the right level of detail or complexity, its value for monitoring is limited. Sometimes there is even a failure to recognize the difference between consumed hours and progress. Failure to use the right schedule can lead to performance issues resulting in late design delivery, over budget delivery, or poor-quality design delivery, or any combination thereof. A well-designed and managed A/E design schedule promotes quick and accurate updates, supports proactive analysis to minimize delays and claims, and aligns with other project controls functions to enable integrated cost-schedule-risk design scheduling. The authors, working for firms that provide engineering design services, have experience in working with the designers to develop the right level of detail for the design portion of a project, to establish a stage-gate approach to design milestones so they can align with cost, schedule, and risk monitoring, and so performance can be accurately measured. The authors bring a wide range of perspectives, from process engineering design scheduling to design-build A/E scheduling, to construction manager (CM) agency A/E monitoring, to CM at risk A/E support scheduling. This article will offer a proven approach that demonstrates guidelines for schedule design, development, monitoring, analysis, updating, and reporting, as well as set the benchmark to facilitate mitigation when necessary. This article was first presented as PS.3427 at the 2020 AACE International Conference & Expo.
Introduction
Design scheduling is handled by several different parties, or parties working in several different roles and contracts. A/Es might work directly for the stakeholder or employer on a project, a contractor in the form of a design-builder, or a contractor working as a concessionaire for a public-private-partnership (PPP or P3).
Background
To discuss this issue, it is important to define design scheduling and establish the value of providing professional critical path method (CPM) scheduling to plan and manage the design process. Many projects fall behind during the design process, in design-bid-build (DBB), design-build (DB), engineering-procurement-construction (EPC), and construction manager at risk (CMAR). Each of these project delivery processes has its own challenges, but design schedule management is a primary one. The complexity of architectural-engineering (A/E) design is mostly because of the variety of disciplines necessary to complete a project, the scope development maturity, and the ability to assess progress in design. At a given stage of design, say 30% design development, the structural design might be at 60% complete, while commissioning might be at 0% complete. Developing a schedule of this sort can be difficult and monitoring can be even more difficult.
What is Design Scheduling?
Design scheduling is the act of planning the design activities, developing a CPM schedule for those design activities, and maintaining that schedule through a regular updating process that captures progress information, assesses performance, predicts trending and delay issues, and provides corrective actions to enable the design to complete all milestones on time.
How is it Commonly Handled?
Typically, A/Es develop and maintain their own progress schedules using different software and methods. Since the schedules are most often not shared with other stakeholders, there is a reduced need for a high level of technical scheduling effort as would more often be seen in the construction process. However, all designs evolve through phases, a series of increasing levels of scope definition, and assign milestones representing the completion percentage at the end of each phase. In many projects, especially the more successful, the milestones act as the gates at which cost and schedule reviews are performed to ensure that the design is progressing and maintaining the original budget and duration established in the conceptual stage. As cost and schedule are verified at each stage, the gate opens and allows design to move into the next phase.
This is often called a stage-gate approach, and studies have shown that when done appropriately, the project is more likely to achieve the design-to-budget goal, defined as ensuring that the design stays within the planned budget as it evolves to full maturity. Meeting this goal is enabled by a formalized process of detailed review at the different levels of scope definition, ensuring that the budget, schedule, and risk issues have been updated and validated. Combined with a good contingency process, this evolving process of projects controls support and verification, helps identify any design issues that are at risk of driving up budgets and extending schedules.
Value of Design Scheduling
Depending on contract type, many projects cannot proceed into procurement and then construction without design progressing as planned. Many projects under DB and EPC delivery methods progress to procurement and or construction without a completed design. EPC or DB project durations tend to be both quite long duration and technically complex projects that often require multiple phases of design. For these projects, the design effort is often scheduled in the CPM schedule. In both cases, design costs are related directly and only to labor, so productivity and production are both important. Issues in design delivery are caused by taking more time than anticipated or quality concerns. Using the stage-gate approach limits both potential sources of over run.
Risks of a Weak Design Schedule
If the A/E does not have a plan for completion of the design within the planned duration, it is unlikely that they will engage the right individuals, or the number of individuals needed, and the design effort will fall behind, ultimately delaying the start of the project.
There are also risks associated with the designers working without project controls monitoring, so the scope of work can grow, or features can be added, since there is no feedback related to the costs of the design, or the feedback comes after the design is complete. This is called scope creep when additional scope is added, often unintentionally, or gold-plating, when the A/E designs more expensive features than originally budgeted, which will increase the costs and duration often unbeknownst to the stakeholders.
Benefits of a Good Design Schedule
A well-designed and managed design schedule will allow the project to meet the stakeholders’ goals in progressing through the project phases into procurement and then construction as scheduled and within budget. Conceptual project schedules will show time allowed for phases of design, producing increasing levels of scope definition or design maturity, until final construction documents are produced.
As design progresses, according to the original schedule, staff work is assigned consistent with the design budget. Senior, more expensive, designers are assigned for the innovative and technical requirements. More junior, less expensive, computer design operators produce the details and production drawings. Each stage-gate milestone receives reviews to ensure compliance with budget, schedule, constructability, value planning, and risk. When done properly, the design matures in a controllable fashion, the stakeholders are aware of the adherence to the goals, and the phase-gate process allows corrective actions when there are deviations from the original benchmarks.
Studies Related to Design Scheduling
The value of this effort is reinforced in a 2014 study, by McGraw Hill, which notes that, “The ability to develop a set of documents that meet the stakeholder’s program requirements and are constructible within budget is unanimously cited as the most-valued metric for design team performance . . .” [page 6, of reference 8]
In the same study, the second highest cause of uncertainty with greatest impact on cost is stakeholder program or design changes and the third and fourth are design errors and design omissions, with the program design changes ranking significantly greater than the design errors/omissions. [page 14, of reference 8] Progressing through the design process with a weak phase-gate process can allow design development that is focused only on the design and not the budget or schedule, making it subject to scope creep. Many design changes can cause delays to other disciplines and hours expended on designing features or even options that may or may not be adopted. Without a phase-gate approach delays to time and budget, due to accumulated changes, can and do go underestimated until the end of the design process causing overruns in budget and/or time. The impact on the schedule can be surprisingly significant since budget overruns that are discovered late in the design process will often create a need for cost reductions. These cost reductions, commonly poorly named as value engineering efforts, can become increasingly critical as the team is trying to get construction work started. Value engineering should take place much earlier in the design process, in fact, it can be done as soon as there are drawings to review and the next step after value planning. However, when the budget is overrun and there is pressure to release construction drawings to start work, what is called value engineering is usually just quality reductions, materials changes, or even scope deletion. A detailed state-gate project controls effort integrated with the design process can help ensure the project is designed to the original budget, or if there are legitimate changes that require budget increases, the stakeholder is notified early enough to minimize impact on the schedule.
Project Delivery Methods Associated with Phases of Design
The type of project delivery method contributes to some of the uncertainties in A/E design since in traditional delivery the A/E has ultimate quality control that is tested by the bid market. In many other delivery methods, the contractor either takes over the design or is intimately involved in monitoring design as it advances through the stages from conceptual to bid or tender documents.
Design-Bid-Build – Complete Design = Stakeholder to 100%
The traditional, private sector project delivery method typically involves three sequential project phases: The design phase, which requires the services of a designer who will be the designer of record for the project; the bid phase, when a contractor is selected; and a build or construction phase, when the project is built by the selected (typically low bid) contractor. This sequence usually leads to a fixed-price contract. [page 3, paragraph 2 of reference 7] In a design-bid-build type delivery method, the stakeholder will be responsible for most if not all aspects of the design.
A risk to a stakeholder with a design-bid-build delivery method is that they warrant the sufficiency of the plans and specifications to which the selected contractor will ultimately build the project. This means the stakeholder/designer will be responsible for any issues that may arise during construction related to errors or omissions in the plans. There is little or no opportunity for the designer and contractor to collaborate during the design phase, which can ultimately contribute to time and cost overruns due to undiscovered design errors. Further, without input from experienced construction expert staff, the design will likely be less constructible and efficient.
These design errors or omissions can often stem from lack of planning during the design. A well-developed stage-gate approach with clearly defined design deliverables helps the teamwork towards distinct achievable interim goals as opposed to three or four major deliverable dates. Also, early involvement of the contractor or construction manager can help to recognize many of these potential issues from a construction point of view. For this reason, part of the stage-gate approach should include constructability review. Constructability reviews are part of the evolution from value planning in pre-design to value engineering and constructability reviews during design as drawings are produced. These quick reviews by construction experienced individuals ensures that designs can be built as they bring eyes of physical, real-world constraints to the design. Questions generated during this process always add value and support a more robust design.
EPC – Stakeholder to ~15%, Contractor to 100%
In the engineering, procurement, and construction (EPC) type of project delivery method used commonly in industrial and process industries, the stakeholder performs studies or research, decides to go forward with a project, determines the results needed from the project, develops the appropriate scope definition to ensure understanding of the stakeholder’s needs, then hands the scope definition over to the selected contractor who proceeds with advancing the conceptual phase design, moving on to feasibility, to front-end engineering and design (FEED), to detail design, then finally to implementation.
Generally, these are lump sum/fixed price contracts. This places the risk of final scope definition and performance on the contractor. In addition, it makes it easier for the stakeholder since managing one contractor is simpler than managing several contractors, and much simpler than interceding in the historical conflicts between contractors and designers. Using an EPC firm will allow for clean lines of communication from the design to construction phases and less mistakes because of the team being unified under one company or contract. The stakeholder must be clear with their goals in the early program and communication throughout the project. Without a clear vision there will be scope ambiguities and potential scope creep and it will be difficult for the EPC firm to plan, monitor, and control the project. The main disadvantage for the stakeholder will be less design control.
The success of the EPC firm will depend on the robustness of their planning and scheduling, which will reduce confusion and conflicts in the field where the costs for rework are much higher than costs of design changes earlier in the process.
Design-Build – Stakeholder to ~30%, Contractor ~30% to 100%
Design-build delivery method in commercial projects is similar to the EPC delivery method, however, this concept is commonly used in many industries outside of the EPC process world, particularly as a means to shorten the construction duration and limit risks to the stakeholder for performance. The stakeholder details the drawings to the point at which it defines the scope of work without eliminating opportunities for innovative design by the contractor. The documents that the stakeholder prepares for use in bidding and procuring the contractors are often called “bridging documents” or the “program definition” documents. The contractor includes the detailed design firm on the DB contractor team, so there is a more engineering-construction integrated approach to design. The contractor can detail the design in specific scopes of work to the point at which it allows construction to proceed, and it accommodates early release of some design packages, advancing the construction. An industry term for this staged release of early trade contract work packages is often called “fast-track” construction, and there are implementations relying on fast-track delivery such as “advanced work packaging” that formalize the effort and helps improve the quality of the transition to construction.
CM at Risk (CMAR) Project Delivery – Stakeholder to 100% with CMAR Providing Project Controls
With CMAR delivery, the CM acts in the interests of the stakeholder, providing project controls expertise and construction experience to help monitor design by VE, constructability reviews, estimating, and scheduling. This allows the CMAR to coordinate with the designers to plan and schedule early trade contractor work in packages that allow construction to start earlier than would be possible with full design required before bidding. This method is commonly contracted on a cost-plus-a-fee in the early stages to enable the CMAR to provide these services, but most often, converts to a fixed fee for a fixed duration contract once the scope definition has advanced sufficiently for an accurate bid. Risks to the stakeholder lie in the reputation and competence of the CMAR, as well as the full engagement of the CMAR in validating the budget and schedule of the design as it matures. However, with an experienced and competent CMAR, the project can sequence trade work and shorten the duration while minimizing stakeholder risk. Once the CMAR is willing to convert to the fixed price and duration, his role is more akin to a traditional general contractor, taking on all the risk of performance.
Alignment of Design Stages and Project Controls with Project Delivery Method
Designs mature through the design phases and so project controls services must track with estimates and schedules aligned by the level of scope definition and the usage of the budget and schedule. The characteristics of the estimates and schedules and the alignment with scope definition are best explained in the AACE International recommended practices for cost and schedule classes. [References 2 and 3, (page 3 in both publications)].
Pre-Design Phase
In the pre-design phase, there are no drawings to define the scope of work. The project is defined by a statement of work or other narrative description of the project. Estimates and schedules are very high-level, providing analogous or parametric level products with a wide range of accuracy to the lack of scope definition. AACE Class 5 estimates are typically provided during this phase, as well as AACE Class 5 schedules. However, these early budgets and schedules are the beginning of the benchmarks against which the project will be monitored and analyzed, so it is vital that pre-design phase estimating and scheduling is appropriate and reasonable.
At this stage, value planning is useful as it helps provide guidelines as the project moves into early design using appropriate techniques and products for the location and industry.
The delivery method at this phase has generally not been determined so the project controls services are typically provided by the stakeholder, whether in-house or by consultant. Engaging the project controls professionals during pre-design provides guidance in selecting an appropriate project delivery method and is a strong indicator of a successful project.
Concept Phase of Scope Definition
In this phase, project controls services continue to be comprised primarily of developing conceptual budgets in the form of capacity factored or parametric modeled AACE Class 5 concept screening estimates, preliminary schedules in the form of AACE Class 5 concept screening milestone schedules, and value planning to help determine the construction means and methods. In some industries, when the professionals providing estimating and project durations have extensive experience and benchmarked databases, the range of accuracy can be narrowed for both budget and schedule, which reduces risks during later phases.
Design Phase
In the preliminary design phase, there are likely to be sketches, plan layouts, line drawings, and site concepts. However, as design progresses through this phase, further development will result in much more detailed drawings. The design phase is divided into sub-phases based on design development progress stages. Good practices suggest that completion of each phase should result in a thorough cost, schedule, risk, and scope review to ensure that the design is progressing satisfactorily and can be built using efficient techniques, at the cost specified in the budget, and within the planned project duration. With the stage-gate process, the design engineering halts until the cost, schedule, risk, and scope review verifies that the design still fits to the budget and project duration.
Concept Development – to 15%
In this phase, project controls services are comprised primarily of developing study budgets in the form of equipment factored or parametric modeled AACE Class 4 estimates [1] for study or feasibility purposes, planning milestone and project events AACE Class 4 schedules [2] for feasibility study purposes. During this phase, scope definition is primarily still the responsibility of the owner.
Design work is an iterative process. As a result of the nature of this work there is a tendency to only want to track hand-offs between disciplines in the schedule for all the phases, especially the conceptual phase. However, the more detail in the inter-discipline relationships, the better. The best practice is to plan for the known scope then adjust as the details become clearer. Tracking only hand-offs never yields an accurate schedule or a schedule that can be tracked and reported on in a valuable way. In schedules that only track hand-offs the logic ends up needing to constantly change to match what is really going on, which is unnecessary work. Planning for the known scope, then making adjustments, also helps in successive phases because the teams may change (and probably will), but if the new team can see what happened in the previous phases in detail, then they can avoid unnecessary rework.
Schematic/Scoping – 15% to 30% (FEED 2 Package)
In the 30% maturity of scope definition, the design phase is likely to be the start of detailed design documents, providing more scope definition. Project controls in this phase are comprised primarily of developing sanction budgets once again in the form of budget authorization AACE Class 4-unit cost and line-item estimates, and more detailed planning AACE Class 3 authorization or sanction schedules [2]. At this point in the scope definition maturity, the responsibility for design depends on the project delivery method, as noted above. However, the discussion here about the project controls services supporting design monitoring may be provided by the owner, the A/E, a consultant to the owner, or the contractor when the delivery is design-build or EPC.
During the approximate 15% to 30% design, commonly referred to the schematic and preliminary design stages of the design, the key opportunity is to ensure the design is beginning to align design deliverables with the construction schedule needs. The CPM schedule can now start to support further refinement of the deliverables and specify how interim design stages will be monitored and tracked. One of the goals and focuses during this stage of scheduling for design should be establishing design definable features of work for the major deliverables.
Establishing these interim design features of work deliverables can help to:
- Define task flow through each major deliverable
- Establish critical path dependencies necessary to drive a design deliverable to completion
- Help alert the project team to specific needs required by one another.
As discussed earlier in this article, key design deliverables are typically tracked to certain percentages throughout the life of the design, but the problem is assigning progress to these percentages. To successfully do this, decisions need to be made as to what percentages apply to disciplines at each stage gate. It is during this stage of design that the designer should include additional design players, i.e., sub-consultants, out-side agencies, or the technical team to collaboratively discuss roles and responsibilities as it relates to the design and schedule. It is important during this early stage to collaboratively agree on interim design delivery milestones to help ensure clear deadlines providing scope definition for each related discipline. These discipline-specific scope definition completion percentages should be used in scheduling.
During the conceptual design stage, a milestone schedule was developed to establish the major deliverables. This stage of design is where the schedule should start to move from conceptual/milestone driven to evolve into a more detailed logically driven schedule that contains these discipline-specific scope definition completion percentages.
See the following list for some possible expected design submittals goals during the 15% and 30% stages that can influence the schedule planning:
15% (Schematic Design)
Develop design draft schematics and concept layouts
Initial opinions of probable construction costs
Determine that the concept is consistent with the design budget
30% (Preliminary Design)
Finalize basis of design and advance spatial design
Design is suitable for an initial constructability review
Begin drafting the project manual
The 30% preliminary design phase is also the stage where not only the design schedule criteria is developed, but the construction implementation of the project should also start to be included in the project schedule. This should help the design team better understand how the project will likely be constructed with insight provided by experienced construction managers (CM). This will of course require involvement of CMs to assist the project team in bringing their construction background to the table. Their input early in the design process will beneficially impact design, ultimately yielding a better, more efficient, and more complete design, as well as promoting early resolution of design problems before impacting the schedule.
Planning to support the design submittal goals occurs during this stage; with products such as contract time determination, schedules used to establish contract delivery dates, and pre-bid contractor’s schedules from a select group of approved contractors to help align the construction with early design. These schedules will need to be reviewed by the stakeholder and are used for confirmation of procurement decisions and to start monitoring progress at the various stages to ensure they are on track either through durations or interim milestones.
Another often overlooked value to the design schedule at this stage is to start to establish critical paths through the design criteria so the CPM schedule can ensure contributing disciplines provide their submittals on time to allow successor design to proceed. This effort will increase in later stages as more detailed designs are developed.
Collaboratively establishing design deliverables will significantly improve the quality and efficiency during this design stage. While this stage of design is still relatively early, construction and schedule input now could lead to significant value engineering savings that would not affect bidding documents.
Design Development – 30% to 50% (FEED 3 Package)
In the 50% maturity of scope definition, the design will be expanded to more detailed drawings in multiple disciplines, requiring considerably more coordination between the disciplines. Project controls in this phase are comprised primarily of developing control budgets in the form of control AACE Class 2 estimates [1] providing detailed unit cost and line-item take-off estimates and bottom-up planning AACE Class 2 schedules [2] for control or bid/tender use. These estimates and schedules are provided by different entities based on the project delivery method. For design-bid-build, the owner still has the responsibility and provides the integrated project controls support, either in-house or with a consultant, for CMAR, the CMAR provides the support sometimes with the owner providing a program or construction manager to validate the results, and with design-build or EPC, the contractor starts to pick up the integrated project controls support to their own design effort. These responsibilities for the integrated project controls services are consistent through the rest of the stages of design maturity.
Construction Documents – 50% to 80%
As the design matures from 50 to approximately 80% complete scope definition, the design is being finalized, disciplines are coordinated in a feedback loop, quality control is implemented with check sets and/or building information modeling with 3D drawings. Project controls in this phase are comprised primarily of developing check estimate budgets in the form of bid/tender Class 1 detailed unit cost with detailed take-off estimates at the same level of detail as contractor bid documents, producing detailed planning Class 2 or possibly Class 1 bid/tender control schedules [2].
Bid/Tender Documents – 80% to 100%
The goal of this design stage is typically to produce a complete set of drawings and specifications that have passed internal quality control and coordination and are ready for construction. The design is suitable for final client review, permit application and allows an opinion of probable construction cost and project contractual duration that will serve for review and selection of the contractor. This is also the stage for a final bid document review to ensure everything aligns with stakeholder and third-party requirements. Lastly, the final goal is to publish the bid documents and supplemental information for the market.
Depending on the project delivery method, the responsibility for completing the design can vary. The scheduling effort during this final stage will help ensure each of the design package criteria is met with all submittals and is complete. Accurately modeling the final stages can ensure all reviews or meetings are scheduled in advance to help ensure a collaborative communication between all design team members or stakeholders.
Recommended Practices for Design Schedule Development
Phase-Gate Approach
The approach that is commonly called a phase-gate approach to project controls support during design has proven success when followed appropriately (Phase Gate is addressed by the Construction Industry Institute in discussions of Front-End Planning effort). This approach uses the design development phases or stages noted above and recommends the use of an approval gate at each stage. When the design has developed to match the stage of scope definition, design is not allowed to proceed until a thorough review of the cost, schedule, risk, constructability, and value engineering shows that the project is still tracking within the target benchmark, opening the gate to allow design to proceed into the next phase up to the next gate.
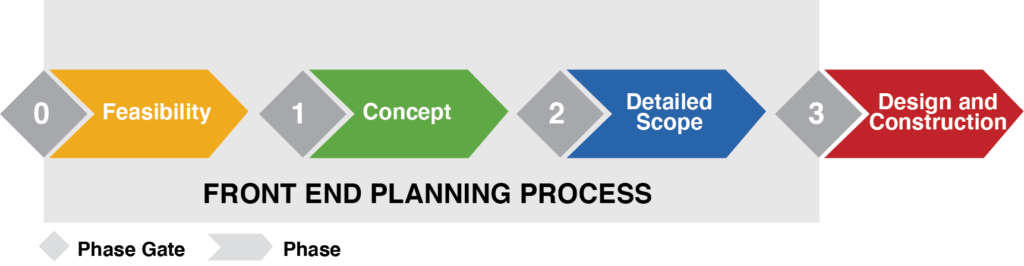
Figure 1–Phases and Gates from CII Front End Planning Process
Clear Program Definition
Clear understanding of the design statement of work or concept write-up is vital to establishing the design definable features of work. This starts with the design package criteria that clearly states each design submittal requirement; “The project will require 500 feet of pipe” is an example of a poorly defined feature. A better-defined example would be that the project requires 500 linear feet of RCP and two drainage structures for adequate site drainage across a specific area.
The scheduling effort will be less effective if the contractual requirements for the schedule are vague and non-specific. Often, the schedule specifications clearly state the requirements for construction, therefore a construction schedule is typically detailed to build the project. So, the question needs to be asked: “Why can’t the schedule specifications require similar level of detail to monitor and track design?”
The schedule specification is the stakeholder’s opportunity to ensure the designer monitors progress appropriately for the full design effort. It is crucial that the design and construction documents are well developed and clearly depict the stakeholder’s needs. This is especially true for design-build, and CM at-risk type deliveries since most of the project risk falls to the contractor, which can limit the reporting to a stakeholder. Generally, the schedule is and will be one of the best communication tools between the designer and stakeholder for all delivery methods. Therefore, a vague or non-specific schedule specification can reduce the accuracy of information provided to the stakeholder. This tends to lead to unreliable schedule predictions as well as over or underreported progress that may lead to late design and design cost overruns. An appropriate schedule specification should address the following items.
Establish Completion Milestones (Phase-Gates)
There is no single standard for the percentage of design completion at each milestone, so it is vital that these are established to accommodate the needs for quality control review, value planning and engineering, constructability review, budget and schedule review, and risk assessment. Sometimes these milestones align with payments or are designed to enable certain package releases. Establishing these milestones is important and should be carefully reviewed by the team to ensure that the scope of design work required by each milestone is defined and understood. With the appropriate definition and team understanding, progress monitoring is improved to allow successful design at the appropriate time for the expected project duration.
Define Detailed Scope Required before Each Milestone (Phases)
Once the phase-gate completion milestones are established, the detailed scope required to be completed in each phase must be identified. There should be milestones for each phase, they could be in the form of deliverables. It may be an approval package or a submittal depending on the phase. The requirements for each milestone must be specifically identified and the level of quality outlined. Note that depending on the project delivery method, the stakeholder responsible for accepting the final design package might be the stakeholder or the contractor.
Document Specific Completion Definitions to Support Project Controls Review
For this approach to work well, it is important that the milestones are well defined so monitoring the completion of each phase-gate milestone is straightforward and simple. This is a tougher problem than it should be because the cumulative percentage of completion for any given milestone includes a wide variety of different levels of completion for many disciplines. While a 30% design completion might show structural design as 60% complete, commissioning may not have even started. No matter how progress is tracked, the definition allows a good estimate and evaluation of completion. The authors have found that resource loading of the schedule using design hours and costs is the best approach when the designer team participates. However, when the designer is not cooperative in establishing discipline hours and costs, there are other simple implementations of progress monitoring, such as earned value based on the number of drawing sheets, which can still be useful. No matter the progress monitoring, the stakeholder must specify completion goals and the designer still must identify which sheets must be complete to achieve the gate milestone terminating each phase.
The scheduler should meet with the designers, get a list of all the disciplines that must be completed to meet the milestones, and then determine with the designers how mature each discipline must be at each milestone. Developing a clear definition of each milestone with detailed understanding of the maturity of each discipline is vital to implementing this approach.
Key Risks in Design Schedule Development
Poor or little validation of the key design milestone completion percentages can often be the primary contributing factor to a design submittal failure. Without the use of a stage-gate approach to scheduling, a design firm’s progress monitoring of design deliverables can be inconsistent and inaccurate. Often one design firm’s definition of 30% drawings is very different from another firm’s idea of the 30% design submittal. Or, after submission of the deliverable, the submitted package is only approvable to 20% complete based on design criteria. These discrepancies can stem from a design firm’s inability to accurately model and track to design submittal deliverables, which can affect cost, time and quality. The following list of questions should be considered when updating and progressing the planning design schedule:
- What is the overall estimated completion percentage for the design package?
- How will the deliverable milestones be measured, by money, or hours expended?
- How are the design definable features of work developed?
- Do the costs and hours in the activities in each submittal requirement equal the total submittal budgeted cost/hour?
- Do the activities clearly define the measurable deliverables?
- What is the level of effort?
- Is the schedule able to monitor the design milestones, i.e., 15%, 30%, 60%, 90%?
The importance of accurately modeling and updating the schedule can significantly increase the reliability for the design submittal deliveries. This is achieved primarily through the appropriate modeling of the activities and managing the stage-gate project controls reviews to reach the overall submittal requirement. By appropriately validating each design submittal milestone completion, potential issues should be identified and an acceptable status for the submittal goal established.
Develop Activity Detail per Milestone
This will help define the specific activities included in the schedule that must be completed before opening the gate to the next phase. This is the area where the A/E input is needed because most A/Es have internal planning documents that suggest the disciplines and the discipline completion that should be associated with each milestone. The scheduler will need to collaboratively acquire this information and then validate it with the A/E team to ensure an appropriate detailed design schedule that models the expected maturity of the individual discipline documents.
Establish Resource Availability
Establishing design resource availability by discipline should be done after activities are identified and sequenced, and then activity durations can be determined. A key part is knowing what is needed (i.e., civil structural architectural (CSA), electrical & instrumentation (E&I), process, plant design, mechanical), as well as knowing what level of resource is needed (i.e., junior/senior level), to provide the expected design development.
Knowing the full design scope is paramount to acquiring the team needed. The next step after establishing the scope is understanding the complexity of the scope to help the designers determine the mix of senior and junior staff needed for the disciplines. Of course, the designers will consider the risks of using junior personnel (i.e. increased durations, quality of work) and evaluate those risks with the costs of more senior staff providing the work.
Once the resources required are known, then the process of modeling staff availability can begin. Once the resources are developed in the scheduling software, the next step is to establish the discipline resource calendars. Later the team’s schedules can be incorporated into the master schedule to ensure that all other required work is planned and monitored, and performance in design work will be sufficient to maintain the program goals.
During the establishing of resource availability, consideration needs to be given to construction equipment availability since the delivery will be a function of the approved design releases for procurement. The design schedule should show any of these or other long-lead procurement items that may have to be ordered or reserved during the design phases to have it in time for the construction. With an accurate design schedule, the stakeholder can determine if the schedule will allow for the selected contractor to order these items or if the tight schedule might require the stakeholder to consider direct purchase. These are decisions that should be evaluated as soon as possible after the design schedule is approved.
Identify Time and Cost Budget (Load Hours and Costs)
Once milestones are defined and resources established, the resource loading is pretty straightforward, except that it has to meet the milestone completion. This requires resource loading the schedule, which is the individual discipline costs and hours broken down into the work that is associated with each milestone definition.
Suggested Practices for Design Schedule Monitoring and Analysis
Enforce the Stage-Gate Approach
Monitoring of design is straightforward once the definitions are set up, so this step simply requires adhering to the project controls services identified for each of disciplines. The stage-gate approach to integrated project controls monitoring of design deliverables is relevant to any of the project delivery methods. No matter whether the delivery is design-bid-build where the owner is at risk for design, or CMAR, where the owner and CMAR collaborate to minimize the risk of design, or design-build and EPC where the contractor takes over and assumes full responsibility for design, the stage-gate approach improves design durations and quality.
Monitor Design Progress at Activity Level
The main goals of accurately modeling and updating a construction CPM schedule are to monitor progress, identify delays early enough to mitigate, provide corrective actions to maintain planned progress, provide change management support, and avoid disputes in construction. With design scheduling, the goals are reduced to monitor progress, provide corrective actions to maintain planned progress, identify changes from the project controls reviews, and provide change management support.
Much of this can be achieved through a combination of critical and near-critical path analysis and CPM schedule trending analysis with design scheduling because design combines a productivity effort with a sequencing effort; multiple teams take on the design concurrently, but each team has cross-discipline relationships with the other teams that drive delays across the disciplines. The trending analysis is most useful in activity performance trending, such as duration overruns and plan adherence monitoring, rather than just sheet count or earned value metric trending. The updated project schedule is the primary monitoring tool for the project. It provides the benchmark for analysis of progress and delays. Review and approval is the stakeholder’s opportunity to ensure a quality update schedule that will serve as the model for analysis of change, trending and completion predictions.
The first step in the update process, prior to any data input, is to gather the data. The scheduler should provide the update report to the team and responsible parties at regularly scheduled intervals based on the frequency of the update process. Suggested information to provide in the update report or layout is: activity identification code, activity name, original duration, remaining duration, percent complete, float, actual start, actual finish, with a blank column for remarks.
One aspect of planning includes assigning specific roles and responsibilities for measuring the progress and performance. During the schedule development process, the scheduler should assign responsibility to each activity in the schedule. In Primavera P6™, this is easily accomplished using an activity code (i.e., responsibility).
Using a responsibility activity code allows the scheduler to break down activity progress by the discipline or individual performing or responsible for the work. Each responsible party can, by organized use of filters and layouts, review a report of work progress and effectively plan for near term activities. The scheduler can then also more easily identify potential issues and mitigate risks based on performance factors.
Use Earned Value Management
Since the design scheduling effort is heavily oriented to production and productivity along with sequencing progress, monitoring is well served with a focus on the productivity and production. A critical and near-critical path analysis ensures that delays are identified when they occur, such as a failure of the architect to provide initial floor plan layout to the structural engineer. Non-critical path delays can also occur, so it is important to monitor the progress of all activities, including non-critical path activities.
The typical failures in design scheduling occur when cross-discipline hand-off dates are missed, progress falls behind, or budgets start to overrun. With performance issues, too often the designer simply redefines a poorly defined milestone to claim completion at the planned level, say 30% completion. But when that milestone has been defined in detail, that redefined 30% completion milestone is identified as more likely 20% or 25% and that has serious ramifications for the range of accuracy of budgets and schedules associated with that phase.
Monitor Hourly Earned Value for Progress
Architectural and engineering design is budgeted and monitored in hours, so loading the schedule with hourly resources is relatively straightforward. There still is a decision to make with respect to budgeting; if the firm has targeted specific designers, then there might be a need to load individual resources, designers by name. This would allow for monitoring to ensure that each person has the appropriate workload and will not be over allocated by the schedule as performance is updated.
More commonly, hourly resources are loaded by roles; grouping individuals by levels or types of roles such as Engineer, Senior Engineer, or perhaps Engineer Level II. The premise is that anyone who carries the title, for the project, of one of the roles is interchangeable with anyone else, so if four Engineers are Senior Engineers, the loading would allow monitoring of over allocation of the group of Senior Engineers.
This role-based approach allows for a certain amount of flexibility and ensures that tasks assigned to Engineers Level I will only be scheduled for the Engineers in that category, so it is easier to maintain the budget. The loading and monitoring is also simplified since specific person performance does not need to be reported.
Monitor Cost Earned Value for Efficiency/Productivity
Although monitoring hourly earned value works well, consumption of hours does not necessarily relate to progress. While it is important to monitor hours, that does not indicate the efficiency of the work, and with the likelihood that there is a range of salaries within each role, the risk is that too many hours are consumed at the high end of the salary range. The design firm needs the ability to recognize when they are at risk of exceeding budget even when operating within the hourly totals for each phase.
This risk can be managed by a loading of costs in addition to the resources into the schedule. The cost-based earned value system can be used to monitor the productivity while the hourly-based system monitors production. Running metrics from both loading will help the design firm stay on schedule and budget.
Provide Critical and Near-Critical Path Analysis
Providing critical and near-critical path analysis is vital as it will ensure that the discipline work that must be sequenced is managed and monitored. For example, the mechanical engineer designing the plumbing system requires multiple input to proceed with 30% preliminary design piping sizing, which might include:
- Plumbing fixture requirements from the architect
- Drainage requirements from the process engineer
- Fuel-fired boiler information from the HVAC mechanical engineer
If the plumbing design cannot proceed without the necessary input, delays from the one discipline can be magnified as other disciplines are unable to complete significant portions needed for the team to meet the 30% preliminary design milestone.
Provide Trending Analysis
Trending analysis is the use of historical records to identify a pattern of production or productivity results that will eventually cause cost and time overruns. These patterns are often insidious and some areas are not easily identified without a detailed schedule used to monitor performance.
An example of schedule trending is the duration overrun risk; if the structural steel engineering has performed the first 25% of their scope in durations that are twice as long as planned, analysis of that trend might show that continued performance at that same rate will cause them to miss a stage-gate by 30 days. Those types of delays will be magnified as they are driven into other disciplines waiting on the structural steel designs, and the trending analysis requires the CPM schedule to determine the expected impact from the delays.
Other trends are more productivity-based only, and could be managed without the schedule, for example, if a project task required 400 sheets of engineering drawings and committed to 40 days to complete engineering, that means the team must complete 10 sheets per day.
If they get 20 days into the task and have completed 100 sheets, they have completed 5 sheets/day. This trends to:
20 remaining days x 5 sheets/day = 100 sheets by day 40
100 sheets (complete) + 100 sheets (trend) = 200 total sheets by deadline
This performance would miss the target by 50%, AND, with proper tracking, scheduling and stage gate milestones the overrun could have been prevented.
Provide Mitigation Needs and Opportunities
One of the benefits of a good scheduling effort is the ability to provide predictive analysis to identify slippage in performance and budget, and the resulting corrective actions that can be recommended to mitigate the delays. Done properly, this can allow the A/E to re-assign resources to supplement or replace weak performers, ensure the right level of experience in each task, and improve the achievement of the assigned level of completion stage.
The same is true of gains; analysis of schedule trending when there are improvements in performance will show potential opportunities to improve delivery dates.
Conclusion
One of the common failures in construction programs is the timely production of architectural and engineering drawings. This shows up as missed partial completion milestones, under-designed milestones, late delivery of completed packages, and the risk of incomplete packages that are released just to meet deadlines.
The further symptoms and risks from this failure revolves around the scheduling and budgeting that is performed at the wrong range of accuracy because the documents are not really completed to the appropriate level of detail in all disciplines. The range of accuracy is dependent upon the maturity level of the documents, so inaccuracy in the level of completion will limit the ability to produce a more accurate project duration (and budget) as the design matures.
A commitment to thorough technical scheduling at a level of detail that allows appropriate monitoring of production and productivity would improve design completion results, with the accompanying improved ability to design-to-budget and schedule. Owners would benefit from requiring and funding an integrated project controls design effort by reduced project durations and lower costs, no matter the project delivery method.
The integrated project controls phase-gate effort has been proven to improve the completeness of the deliverables and the confidence in the measured level of maturity of those deliverables. [5]
While studies related to design performance rarely isolate scheduling of the design, CII has a number of studies of assessments for measuring project scope definition and alignment between project participants that have a strong scheduling component for design stages. One of those studies notes that the index “allows its users to measure the level of scope definition and to compare scope definition to anticipated project success.” This study looked at a Project Definition Rating Index (PDRI), comprised of a number of contributing factors which included the scope definition and appropriate maturity of the scope supported by design scheduling, and found an average “Schedule reduction by 13 percent” in the projects scoring higher in pre-project planning (all the design leading to detailed engineering). [4]
This commitment to an accurate and detailed technical design schedule requires time and costs to develop and monitor the schedule, but the authors have seen huge losses to A/E firms due to designs that take considerably longer than planned and lead to unhappy stakeholders. The costs to provide an integrated stage-gate project controls effort are much less than many of these losses. All the stakeholders, whether owners, contractors, or designers, would see benefits from spending the additional costs up front to provide this effort.
REFERENCES
- AACE International Recommended Practice No. 18R-97, “Cost Estimate Classification System – As Applied in Engineering, Procurement, and Construction for the Process Industries”, Revised March 1, 2016.
- AACE International Recommended Practice No. 27R-03, “Schedule Classification System,” Revised November 12, 2010.
- AACE International, Recommended Practice 56R-08, “Cost Estimate Classification System —As Applied in Engineering, Procurement, and Construction for the Building and General Construction Industries,” Revised August 7, 2020.
- Construction Industry Institute, “Pre-Project Planning Tool: PDRI for Buildings,” 1999.
- Construction Industry Institute, CII Research Team 331, “Assessing the Maturity and Accuracy of Front End Engineering Design (FEED) to Support Phase-Gate Approvals,” 2017.
- C.R.T. 331, “Assessing the Maturity and Accuracy of Front End Engineering Design (FEED) to Support Phase-gate Approvals,” Construction Industry Institute (CII), Austin, 2017.
- DBIA, “Choosing A Project Delivery Method, A Design-Build Done Right Primer,” Design-Build Institute of America, 2015.
- S.M. Report, “Managing Uncertainty and Expectations in Building Design and Construction,” McGraw Hill Construction, 2014.
ABOUT THE AUTHORS
Christopher W. Carson, CEP DRMP PSP FAACE, is with Arcadis U.S., Inc. He can be contacted by email at: chris.carson@arcadis.com
Aaron Fletcher, PSP, is with Arcadis U.S., Inc. He can be contacted by email at: aaron.fletcher@arcadis.com
Noah A. Jones, PSP, is with Arcadis U.S., Inc. He can be contacted by email at: njones@schiavone.net
Leo Carson-Penalosa is with Burns & McDonnell. He can be contacted by email at: carson.penalosa@gmail.com
Rate this post
Click on a star to rate it!
Average rating 5 / 5. Vote count: 18
No votes so far! Be the first to rate this post.
Very interesting.
Excellent article, very complet. Thank you for sharing.
Regards